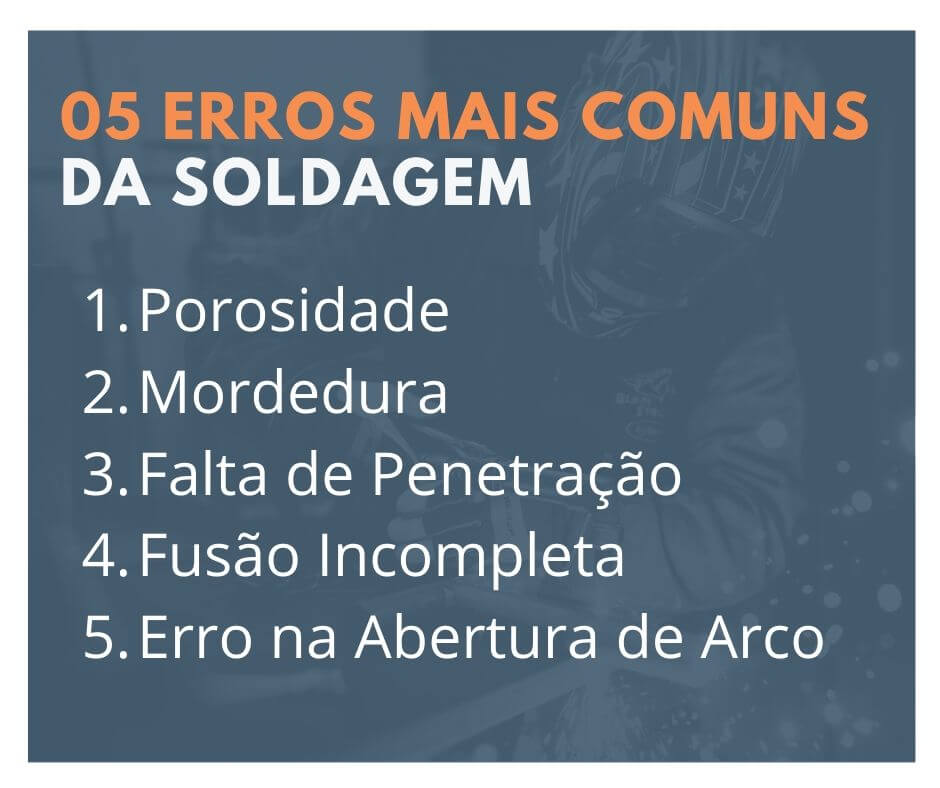
A IMPORTÂNCIA DA INSPEÇÃO DE SOLDAGEM
Ao realizar a inspeção de uma soldagem, os inspetores trazem consigo uma responsabilidade dupla: com as empresas em que trabalham e também com o público em geral.
Eles sabem que as soldas precisam ser de qualidade, pois uma soldagem fora das normas pode resultar em danos materiais e físicos.
Desta forma, os inspetores estão sempre desenvolvendo e aprimorando sua capacidade de detectar e dimensionar defeitos. Esta aprendizagem leva anos e deve ser constante.
Neste ebook, vamos acompanhar quais são os 5 erros mais comuns que os inspetores de soldagem encontram. Eles podem ser facilmente observados e prevenidos e/ou corrigidos.
Ainda assim, o olhar técnico é imprescindível. Os inspetores identificarão problemas, dos mais simples ao mais complexos, valendo-se de técnicas e ferramentas específicas.
1 - POROSIDADE DA SUPERFÍCIE - ERRO SOLDAGEM
A porosidade se dá basicamente pela falta de gás, resultando na formação de pequenas cavidades. A porosidade reduz a “força” da solda. Inspetores de soldagem que não são treinados em testes não-destrutivos estão limitados à visualização de superfícies de soldagem. Mesmo que nem todas as formas de porosidade podem ser detectadas, as que se estendem até a superfície podem.
Essa porosidade superficial pode ser causada por várias razões:
- Quando os metais de enchimento e os eletrodos não foram devidamente manipulados;
- Processos que utilizam gás de proteção, pois podem criar a porosidade se o gás estiver contaminado ou se o fluxo não estiver regulado para a vazão adequada;
- Soldadores que não estão utilizando a técnica mais adequada.
A porosidade pode se apresentar de duas formas: poros isolados e poros agrupados.
Em alguns casos de poros isolados é possível remover apenas a parte danificada e realizar uma ressoldagem. Já para poros agrupados, recomenda-se remover e refazer todo o cordão de solda.
2 - MORDEDURA - ERRO SOLDAGEM
A mordedura é uma descontinuidade superficial que ocorre na lateral do cordão de solda, uma erosão causada pelo metal base na interface da solda. Isso pode causar falhas prematuras de uma peça ou estrutura. Ela ocorre quando muito metal base é absorvido pela região da solda.
Os inspetores de soldagem podem usar uma variedade de ferramentas para detectar a mordedura. Uma das maneiras mais rápidas e simples é utilizando um calibre de solda.
Basta arrastar o calibre transversalmente pela solda. Se ele ‘emperrar’ em algum canto, pode ser uma mordedura.
Uma vez detectado, ele deve ser medido para determinar se é aceitável ou não. Isso pode ser feito com o próprio calibre, por um comparador óptico, um medidor de laser ou outros tipos de medidores de soldagem especiais.
Em casos de mordedura, a melhor ação a se tomar é a de desbastar (remover a parte superior ou o excesso do cordão de solda) e aí sim soldar novamente. Ressoldar por cima da mordedura não é indicado.
3 – FALTA DE PENETRAÇÃO - ERRO SOLDAGEM
A falta de penetração é uma descontinuidade que ocorre quando a solda não se prolonga através da totalidade da junta que foi soldada. Pode ser causada por parâmetros de soldagem incorretos e/ou por uma fraca técnica de soldagem.
A penetração mal realizada prejudica a solda de várias formas:
- A interface entre a solda e o material base não fundido pode ter uma geometria acentuada, atuando como um concentrador de tensão;
- O espaço pode armazenar organismos e materiais estranhos que podem causar corrosão rápida;
- Há uma influência negativa na força da junta de solda, pois a espessura total do material de base não foi unida.
Ela pode ser detectada visualmente quando a soldagem só ocorre em um lado da junta de solda e há acesso visual ao lado da raiz.
Não pode ser detectada visualmente se não houver acesso ao lado da raiz da junta ou se a soldagem ocorrer de ambos os lados e a penetração incompleta estiver no meio da articulação.
As ferramentas que os inspetores de soldagem usam para determinar se existe uma penetração incompleta da junção incluem borescópios, espelhos e lupas. Caso detectada, é necessário remover todo o cordão de solda e retrabalhar a peça.
4 – FUSÃO INCOMPLETA - ERRO SOLDAGEM
A fusão incompleta, ou falta de fusão, ocorre quando o metal de solda não se junta completamente com o material de base durante a soldagem.
Ela pode reduzir a força da solda drasticamente porque não há ligação metalúrgica entre o metal de solda e o metal de base onde a fusão incompleta está presente.
A falta de fusão também pode ser um concentrador de tensão e apresentar taxas de corrosão localizadas mais altas que as partes da solda que não possuem fusão incompleta.
Ela pode ser detectada visualmente por um inspetor de soldagem se ocorrer na superfície da raiz ou na face da junta de solda. Porém, é possível que ocorra dentro da junta da solda, exigindo meios não destrutivos para detectá-la.
Para detectar falta de fusão, os inspetores de soldagem podem procurar perfis incomuns de grânulos de solda, além de verificação com o calibre de soldagem.
A falta de fusão pode ser causada por muitos fatores. Técnica de soldagem e parâmetros inadequados são alguns deles.
5 – ABERTURA DE ARCO - ERRO SOLDAGEM
As aberturas de arco são marcas na estrutura que está sendo soldada fora da zona de solda. São criadas pela descarga rápida acidental de um arco elétrico e podem ter grandes resultados negativos.
Uma vez que uma abertura de arco é tipicamente pequena e acontece rapidamente, o volume do material de base que recebeu a abertura aquecerá e esfriará rapidamente.
Isso pode resultar na formação de uma microestrutura extremamente dura e quebradiça que é propensa a o desenvolvimento de trincas.
As aberturas do arco também normalmente deixam um recuo no material de base. Isso pode ser um concentrador de tensão e também pode tirar a espessura original do material, reduzindo sua força.
Elas podem ser facilmente detectadas por um inspetor de soldagem, desde que o acesso visual à superfície do material de base não seja obstruído.
NORMAS REGULAMENTADORAS DE SOLDAS
Como dissemos no começo, uma solda mal realizada pode trazer danos materiais e físicos, causando prejuízos para o soldador, para a empresa, para o público em geral e até para o meio ambiente.
Em razão disto, existem diversas normas regulamentadoras com a função de garantir a boa qualidade de uma soldagem, evitando assim problemas futuros.
Algumas delas são:
- ASME Boiler and Pressure Vessel Code: vasos de pressão;
- API STD 1104 - Standard for Welding Pipelines and Related Facilities: tubulações e dutos na área de petróleo;
- AWS D1.1 e AWS D1.2 - Structural Welding Code - Steel and Aluminum: estruturas soldadas de aço carbono e de baixa liga / alumínio;
- DNV - Rules for Design, Construction and Inspection of Offshores Structures: regras para desenvolvimento, construção e inspeção de estruturas marítimas de aço.
Há, ainda, diversas entidades responsáveis por definir normas dentro de sua área de abrangência como a Associação Brasileira de Normas Técnicas (ABNT), International Organization for Standardization (ISO), American Welding Society (AWS) e Association Française de Normalisation (AFNOR).