Por que pré-aquecer uma soldagem?
O pré-aquecimento reduz o risco de rachaduras no metal de solda e na zona afetada pelo calor (ZAC) ao:
• Baixar a taxa de resfriamento da solda, impedindo a formação de metal de solda quebradiço, além de permitir mais tempo para que o hidrogênio escape da solda fundida;
• Remover a umidade (fonte de hidrogênio) da peça;
• Reduzir o encolhimento ao diminuir o diferencial de temperatura.
• Remover a umidade (fonte de hidrogênio) da peça;
• Reduzir o encolhimento ao diminuir o diferencial de temperatura.
Confira o vídeo que fizemos sobre este equipamento:
Pré-aqueça ou não?
O requisito e o nível de pré-aquecimento do aço é determinado pelo código de soldagem e depende da entrada de calor da solda, composição química do aço (carbono equivalente), espessuras, hidrogênio difusível, etc.
Os materiais não ferrosos geralmente requerem pré-aquecimento devido à alta condutividade térmica.
O pré-aquecimento pode ser realizado usando os seguintes métodos:
• Aplicando chama direta - superfície da peça aquecida e, em seguida, calor conduzido através da peça, chama aberta.
• Colocação da peça em um forno - aquecimento uniforme da peça completa, se houver tempo suficiente fornecido no forno, limitações de uso devido ao tamanho do forno.
• Cobertores elétricos - superfície da peça aquecida e, em seguida, calor conduzido através da peça.
• Aquecimento por indução usando mantas - calor gerado por correntes eletromagnéticas dentro do material.
• Colocação da peça em um forno - aquecimento uniforme da peça completa, se houver tempo suficiente fornecido no forno, limitações de uso devido ao tamanho do forno.
• Cobertores elétricos - superfície da peça aquecida e, em seguida, calor conduzido através da peça.
• Aquecimento por indução usando mantas - calor gerado por correntes eletromagnéticas dentro do material.
Dos métodos acima, o aquecimento por indução fornece os resultados mais consistentes e rápidos, além de permitir o controle preciso da temperatura.
É também o método mais seguro e eficiente em termos energéticos.
A temperatura é medida na peça de trabalho usando termopares, pastéis de temperatura ou pirômetros infravermelhos.
As posições de medição são especificadas por códigos de soldagem e são tipicamente dependentes da espessura e geometria da junta.
A Aventa possui o equipamento ProHeat 35 da fabricante americana Miller, junto de seus acessórios necessários, incluindo cobertores/mantas, cabos e termopares disponíveis para locação.
O ProHeat 35
Muito utilizado na indústria petroquímica e de construção e reparação de tubulações, o ProHeat 35 é considerado um dos melhores – se não o melhor – sistema de aquecimento por indução do mundo. Suas características o tornam um equipamento fácil de operar e de alto desempenho.
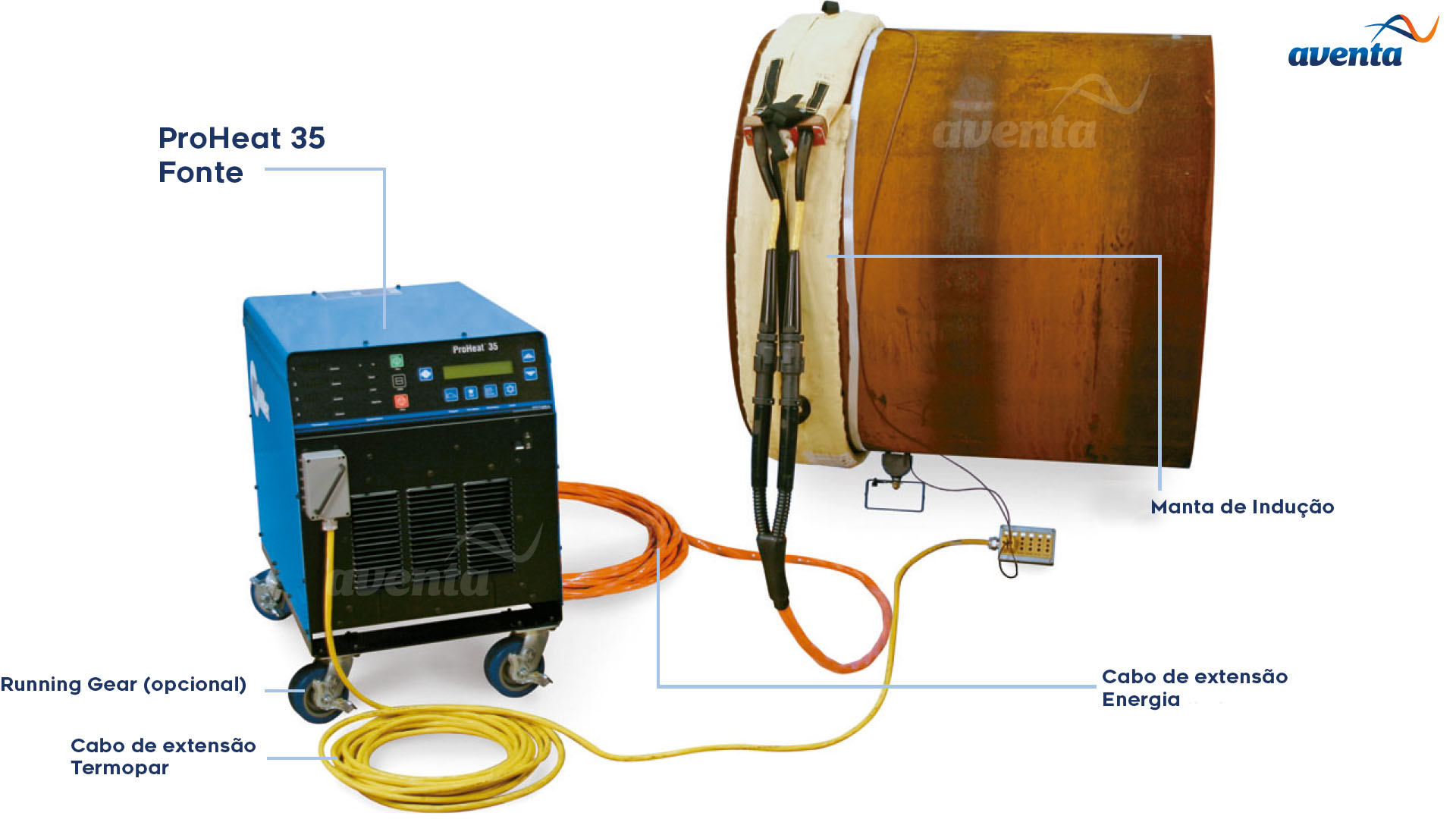
• Fácil de instalar;
• Baixos custos com consumíveis. Sem custos de combustível e custos mínimos de isolamento. O isolamento é reutilizável e pode ser usado 50 vezes ou mais, reduzindo o custo de descarte e substituição.
• Controle de temperatura no painel permite programação manual ou pré-definida;
• O aquecimento uniforme é mantido através da zona de calor, usando indução para aquecer dentro do material. A superfície da peça não é prejudicada pelo calor localizado em temperaturas mais altas do que as especificadas.
• O tempo para alcançar a temperatura é mais rápido do que os processos convencionais devido ao método de aplicação do calor, reduzindo o tempo do ciclo de aquecimento.
• O ambiente de trabalho é melhorado. Os soldadores não estão expostos a chamas abertas, gases explosivos e elementos quentes, associados ao aquecimento de gás combustível e aquecimento por resistência.
• Sistemas de alta eficiência energética (mais de 90% de eficiência) transferem mais energia para a peça, diminuindo os tempos de aquecimento e melhorando a eficiência de energia (consumo de corrente inferior a 60 amp).
• Equipamento portátil.
• Baixos custos com consumíveis. Sem custos de combustível e custos mínimos de isolamento. O isolamento é reutilizável e pode ser usado 50 vezes ou mais, reduzindo o custo de descarte e substituição.
• Controle de temperatura no painel permite programação manual ou pré-definida;
• O aquecimento uniforme é mantido através da zona de calor, usando indução para aquecer dentro do material. A superfície da peça não é prejudicada pelo calor localizado em temperaturas mais altas do que as especificadas.
• O tempo para alcançar a temperatura é mais rápido do que os processos convencionais devido ao método de aplicação do calor, reduzindo o tempo do ciclo de aquecimento.
• O ambiente de trabalho é melhorado. Os soldadores não estão expostos a chamas abertas, gases explosivos e elementos quentes, associados ao aquecimento de gás combustível e aquecimento por resistência.
• Sistemas de alta eficiência energética (mais de 90% de eficiência) transferem mais energia para a peça, diminuindo os tempos de aquecimento e melhorando a eficiência de energia (consumo de corrente inferior a 60 amp).
• Equipamento portátil.
Além disso, o sistema de indução ProHeat apresenta redução de custos em relação aos métodos convencionais por:
• Economia na mão de obra: o tempo de configuração e o tempo para alcançar a temperatura definida são mais rápidos;
• Melhora da qualidade: ausência de rachaduras oriundas de aquecimento não uniforme, além de que o ciclo não precisa ser refeito por conta de falha ou contatores quebrados.
• Mais seguro: não expõe os colaboradores a riscos e não libera partículas perigosas no ar.
• Melhora da qualidade: ausência de rachaduras oriundas de aquecimento não uniforme, além de que o ciclo não precisa ser refeito por conta de falha ou contatores quebrados.
• Mais seguro: não expõe os colaboradores a riscos e não libera partículas perigosas no ar.