As trincas no processo de soldagem ocasionadas pela presença de hidrogênio no cordão de solda e áreas afetadas pelo calor são bem conhecidos há muitos anos.
As trincas causadas pela presença de hidrogênio aumentam à medida que a resistência do aço aumenta.
Os altos custos de combustíveis impulsionaram a demanda por metais mais leves no setor de transporte rodoviário e construção naval. Não suficiente, o aumento das regulamentações do petroquímico levou a necessidade de maiores fatores de segurança.
Como resultado desta situação, exige-se cada vez mais metais com maior resistência e leveza.
Essa pressão por aços de maior resistência resultou na necessidade de processos e consumíveis com a menor presença de hidrogênio possível.
Hidrogênio em trabalhos ao ar livre é inevitável.
Quase todos os compostos orgânicos contêm hidrogênio - tudo, desde lubrificantes e óleos a substâncias naturais no campo e umidade na atmosfera.
As trincas causadas pelo hidrogênio disperso e as zonas de calor afetadas são uma das maiores ameaças à integridade das aplicações de soldagem de tubulações de transmissão (assim como muitas outras aplicações de solda).
Os contratantes de soldagem de tubulação precisam ser proativos na mitigação do hidrogênio na zona de soldagem - e isso começa com o entendimento das muitas fontes de hidrogênio e como eliminá-las ou minimizá-las.
Vamos nos aprofundar sobre as trincas causadas por hidrogênio e fragilização pelo hidrogênio, apresentando as melhores práticas para gerenciar essa ameaça assim como fornecer precauções específicas para diferentes graus de aço e metal de adição.
Como sempre, os procedimentos de soldagem prescritos na aplicação devem ser seguidos. O conteúdo deste artigo pretende ser educacional e não serve como um substituto para os procedimentos e qualificações de procedimentos estabelecidos.
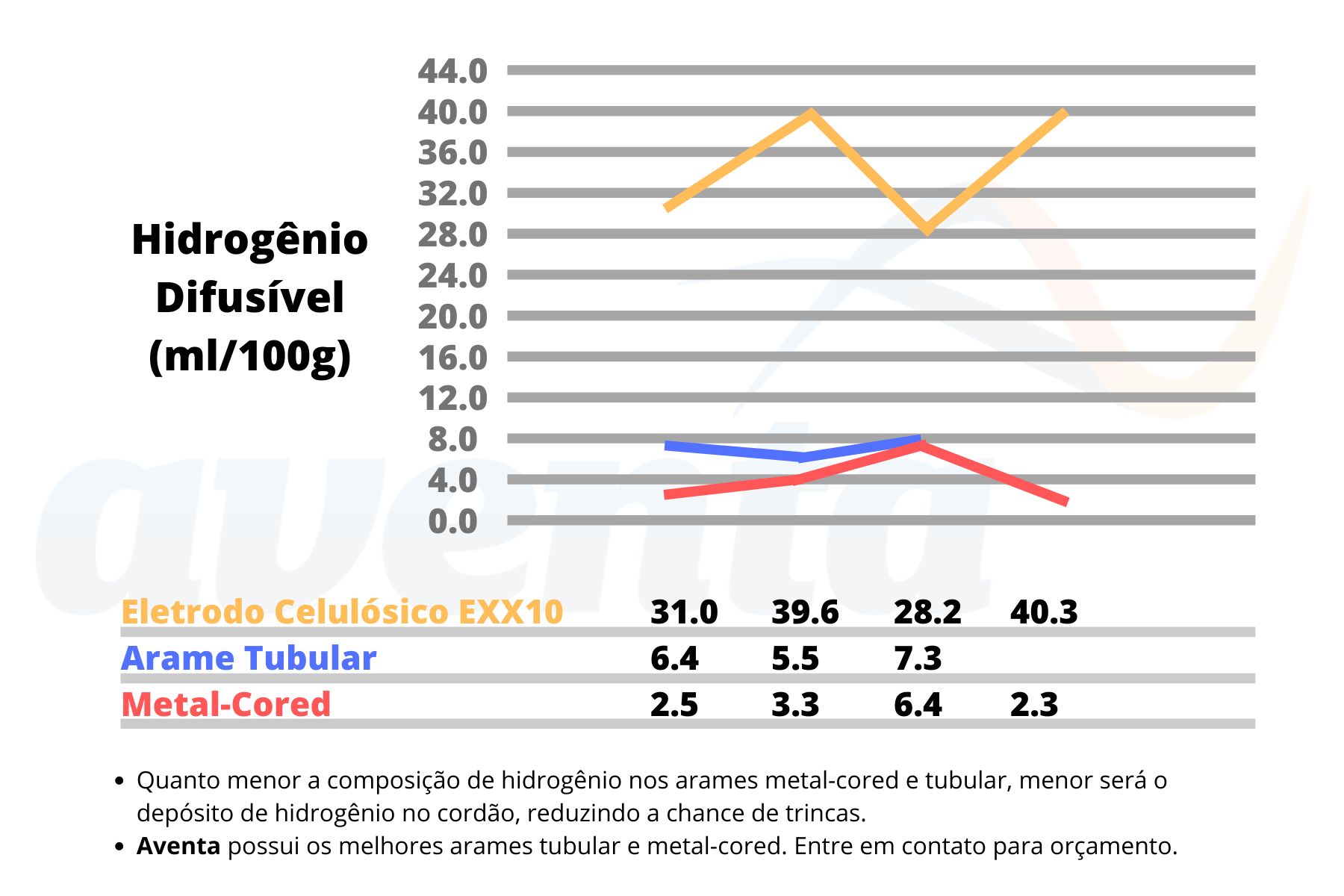
O problema do hidrogênio na soldagem
As trincas por hidrogênio, também conhecidas por trinca a frio, pode demorar horas ou dias após a conclusão da solda para aparecer, o que pode resultar em reparos e retrabalho custoso e tempo de inatividade.
Os íons hidrogênio são extremamente pequenos e altamente móveis, e podem facilmente se difundir para fora da zona de solda e coalescer ao longo das descontinuidades presentes na microestrutura.
Os íons hidrogênio podem se recombinar para formar gás hidrogênio, estressando ainda mais a microestrutura. Essas coleções, ou bolsões, de hidrogênio acabam criando tensões que podem levar a rachaduras.
Para que a trinca de hidrogênio ocorra, vários fatores devem estar presentes. Isso inclui:
-
microestrutura suscetível a trincas;
-
presença de tensões residuais;
-
presença de hidrogênio.
Em geral, a suscetibilidade a trincas por hidrogênio aumenta à medida que a resistência do metal base aumenta.
Reduzir a quantidade de hidrogênio difusível e tomar medidas para reduzir ou eliminar tensões residuais diminuirá as chances de trincas por hidrogênio difusível.
Isso pode ser conseguido usando metais de baixo teor de hidrogênio, melhorando o aquecimento pré e pós-solda (conheça aqui o sistema ProHeat 35 aqui), mantendo as temperaturas entre passagens e, em alguns casos, alterando o processo de soldagem.
Simplesmente prestar mais atenção aos métodos de manuseio e armazenamento de materiais para impedir a absorção de umidade ajudará bastante na prevenção de rachaduras assistidas por hidrogênio.
O problema do metal de enchimento
Uma das principais fontes de hidrogênio na solda é o metal de adição.
A composição do metal de adição, assim como o ambiente e o modo de armazenamento do metal de adição podem afetar os níveis de hidrogênio no metal de adição e no metal de solda resultante.
- Os eletrodos revestidos fornecem os mais altos níveis de hidrogênio dos metais de adição comumente usados em aplicações de tubulações de transmissão, com níveis que excedem em muito 16 ml por 100 g de metal de solda.
- Eletrodos Revestidos de baixo hidrogênio, com as designações H4 e H8, também estão disponíveis e fornecem menos de 4 e 8 ml de hidrogênio por 100 g de metal de solda, respectivamente.
- Infelizmente, os eletrodos de baixo hidrogênio não oferecem as mesmas características de penetração e desempenho que os eletrodos revestidos celulósicos e geralmente não são aceitáveis para a soldagem de tubos com passagem de raiz.
- A transição para um processo de soldagem com arame metal-cored (conheça os arames metal cored Hobart Brothers) para a passagem da raiz pode reduzir os níveis de hidrogênio para 4 ml por 100 g de metal de solda ou menos, enquanto um processo com arames autoprotegidos para passe de preenchimento permite o uso de um metal de adição que é tipicamente menor que 8 ml por 100 g.
- Os arames tubulares também apresentam um número de “sequestradores” de hidrogênio, como compostos de fluoreto, que combinam com hidrogênio para removê-lo da solda.
- Esses arames são particularmente adequados para aços de alta resistência, que tendem a ser mais propensos a trincas por hidrogênio.
Conclusão: use um metal de adição que contenha o nível mais baixo de hidrogênio difusível e seja capaz de atender às propriedades mecânicas desejadas.
Cuidados com Consumíveis para Evitar o Hidrogênio
Todo o metal de adição deve ser armazenado em uma área limpa e seca e deve permanecer na embalagem original até o momento do uso.
- Manter o metal de adição selado ajuda a impedir que a umidade entre na embalagem e a degradação do metal de adição.
- Minimizar ou eliminar a transferência dos metais de enchimento de ambientes frios para quentes também ajudará a minimizar a condensação, que adiciona hidrogênio.
- Se um metal de adição for movido de um conjunto de condições ambientais para outro, ele deverá ser protegido do ambiente e permitir que o tempo normalize à temperatura ambiente do local de trabalho.
- Para aplicações com núcleo de metal ou fluxo, o carretel de arame deve ser coberto e / ou removido e colocado em sua caixa original no final do dia.
- Alimentadores do tipo mala de viagem totalmente fechados também podem ser usados para selar totalmente o fio do ambiente.
- Os metais de enchimento devem ser manuseados com luvas limpas e secas sempre que possível. Suor, óleos e sujeira nas mãos podem ser facilmente transferidos para a superfície do fio ou eletrodo e introduzir hidrogênio e contaminantes adicionais na solda.
Eletrodos Revestidos e o Hidrogênio
Os eletrodos revestidos celulósico (classificações EXX10 e EXX11, como E6010) apresentam um conjunto único de desafios relacionados ao hidrogênio.
Eletrodos celulósicos são comuns em aplicações de tubulações e nunca devem ser armazenados em um forno de eletrodos. Eles devem ser armazenados em temperatura ambiente, protegidos do meio ambiente.
- A umidade presente nos eletrodos celulósicos cria características específicas do arco. Durante a soldagem, a celulose quebra no arco e é uma fonte de carbono, hidrogênio e oxigênio na piscina de solda.
- Os fabricantes entendem essa quebra e formulam os eletrodos para fornecer uma química específica do metal de solda, levando em consideração as reações químicas que ocorrem no tanque de solda derretido.
A secagem do revestimento do eletrodo celulósico altera a composição e pode levar a trincas do metal de solda.
Embora o hidrogênio seja geralmente indesejável, nunca se deve secar um eletrodo celulósico para remover a umidade fabricada no eletrodo.
Se um eletrodo celulósico usado em aplicações de tubulação se molhar, ele deve ser descartado e não deve ser recondicionado secando-o em um forno com haste.
- Da mesma forma, se um eletrodo celulósico ficar muito seco, seja por secagem inadvertida em um forno de eletrodo ou por exposição a clima quente e seco, ele também deverá ser descartado.
- Soldagem de tubos de alta resistência com eletrodos celulósicos deve ser evitada sempre que possível. Se forem tomadas as devidas precauções, esses eletrodos geralmente são aceitáveis e geralmente são usados em tubulações X60 e de menor resistência.
- Às vezes, são usados em tubulações da classe X70, mas não são a melhor opção para aços de alta resistência (algumas empresas operacionais não permitem seu uso acima da X65).
- Embora os eletrodos não devam ser armazenados em fornos de eletrodos, os eletrodos de baixo hidrogênio (aqueles das designações EXX18, EXX15 e EXX16, como E7018) devem sempre ser armazenados em recipientes hermeticamente fechados ou em fornos de eletrodos.
Certifique-se de seguir as recomendações do fabricante para armazenamento e recondicionamento de eletrodos com baixo teor de hidrogênio.
A Importância do Aquecimento Pré-solda, Pós-solda e Entre Passe
O hidrogênio difunde de maneira ideal dos aços usados na construção de tubulações de transmissão a temperaturas iguais ou superiores a 121 graus Celsius.
O rápido aquecimento e resfriamento do metal base, que ocorre durante a soldagem, pressiona a peça e pode estimular a criação de estruturas de grãos duras e fortes, suscetíveis à fragilização por hidrogênio.
O resfriamento rápido oferece menos oportunidades para o hidrogênio se difundir da solda e das áreas afetadas pelo calor, podendo levar a rachaduras.
Manter alta temperatura necessária de pré-aquecimento e entre passe é essencial, tanto para a produção de uma microestrutura mais suave e menos suscetível a trincas quanto para permitir que o hidrogênio se difunda do metal de solda e da zona afetada pelo calor.
Em alguns casos, pode ser necessário aplicar uma tratamento pós-solda (normalmente 24 a 48 horas a 100 - 200 graus Celsius) para reduzir ainda mais a quantidade de hidrogênio que está retido na solda.
O alívio de tensão através do tratamento térmico pós-soldagem pode ser recomendado para alguns tipos de aço.
Aquecimento à moda antiga: Chamas e Oxi-combustível
Muitas aplicações de soldagem de tubulação dependem de tochas de oxi-combustível ou propano à moda antiga (chama) para trazer a junta de solda à temperatura.
- Esse equipamento pode representar um problema, pois a maioria dos gases combustíveis são hidrocarbonetos e o processo de acender a tocha e aplicar a chama ao tubo introduz realmente o hidrogênio na junta de solda.
- O aquecimento com uma tocha também não garante um aquecimento uniforme em toda a junta e na área de calor ao redor, levando a áreas frias que podem aquecer e resfriar a taxas não controladas.
- Da mesma forma, se a junta cair abaixo da temperatura mínima da passagem intermediária, a soldagem deve ser interrompida e a junta deve ser reaquecida aplicando a tocha à junta.
- A medição de temperatura geralmente é um método manual que é deixado para o soldador ou o ajudante do soldador.
Aquecimento por Indução: Melhor Alternativa
O aquecimento por indução é recomendado como uma ótima forma de evitar o hidrogênio difusível por meio do aquecimento uniforme em toda a peça.
- Também é mais seguro que o aquecimento com uma chama aberta (as serpentinas de aquecimento por indução na verdade não esquentam) e fornece um tempo de temperatura mais rápido do que outros métodos de aquecimento.
- O calor é induzido na peça, colocando-o em um campo magnético alternado criado por cabos de aquecimento por indução resfriados a líquido ou a ar.
- Os cabos de indução são enrolados em torno da peça e criam correntes de Foucault dentro da peça para gerar calor.
- Dispositivos de gravação automatizados podem ser integrados ao sistema, o que cria um registro permanente mostrando que as sequências apropriadas de aquecimento/resfriamento foram realizadas.
O fator chave aqui é o controle.
- O operador do sistema controla a velocidade de aceleração, a temperatura de passagem e a imersão pós-solda ou o alívio de tensão com parâmetros exatos.
- Isso controla o resfriamento e garante que as áreas afetadas pelo calor e a solda retenham as propriedades mecânicas desejadas e, ao mesmo tempo, auxiliam na remoção do hidrogênio difusível.
- Esse controle é particularmente importante ao soldar eletrodos revestidos celulósico que introduzem níveis mais altos de hidrogênio na solda e em aços mais grossos e de alta resistência, geralmente menos dúcteis e com menor probabilidade de ceder, causando tensões, fazendo com que o aço ainda mais suscetível a rachaduras assistidas por hidrogênio.
Confira abaixo uma série de curtos vídeos muito explicativos desse processo.
Práticas de soldagem para reduzir o hidrogênio
Embora não sejam ferramentas primárias na redução de hidrogênio, existem algumas mudanças na técnica de soldagem que podem ajudar a reduzir a quantidade de hidrogênio que entra na solda.
- No caso de arames sólidos, metal cored ou tubular, a soldagem com uma distância maior do bico de contato à peça (dentro da faixa recomendada) pode ajudar a remover o hidrogênio da área de solda.
- A maior aderência elétrica resulta em maior pré-aquecimento do consumível e queima grandes quantidades de hidrogênio antes que ele atravesse o arco e transfira para a poça de solda.
- Demonstrou-se que uma diferença de 1/8 de polegada na tensão elétrica pode ter um efeito substancial no hidrogênio difusível.
- No entanto, o stick-out pode aumentar o risco de perda de gás de proteção e levar a outros problemas, incluindo penetração reduzida e baixa operacionalidade.
Como consequência, é importante manter os parâmetros de solda elétrica e outros parâmetros de solda dentro das faixas recomendadas pelo fabricante.
Outras fontes comuns de hidrogênio
Óleos de corte residuais de chanfros, tintas e certos revestimentos aplicados ao tubo, bem como materiais orgânicos apanhados no campo, como sujeira, ferrugem ou óleo, todos introduzem hidrogênio na solda.
- A preparação da junta é crítica: os soldadores devem moer as superfícies interna e externa do tubo a uma polegada da junta para impedir que qualquer um desses contaminantes entre na poça de fusão.
- Cuidado com a condensação e a umidade dentro e ao redor da junta de solda.
- Essa umidade pode ser o resultado de variações de temperatura ao longo do dia, alta umidade ou outros fatores ambientais.
- Especificamente, se a temperatura ambiente cair abaixo do ponto de orvalho (por exemplo, durante a noite), a umidade se condensará nas superfícies expostas.
- Sempre verifique se a junta está completamente seca antes da soldagem.
- Os processos de soldagem que requerem um gás de proteção podem apresentar desafios adicionais por contaminação de gás ou vazamento de mangueiras e conexões que aspiram o ar e, assim, puxam o hidrogênio da atmosfera para o gás.
- Todas as conexões e acessórios de gás de proteção devem ser verificados regularmente.
Conclusão: o foco nas práticas de soldagem com baixo teor de hidrogênio deve ser uma prioridade.
Essas práticas incluem um foco no manuseio adequado dos tubos e dos metais de adição, selecionando metais de baixo teor de hidrogênio e aquecimento adequado de pré-soldagem, pós-soldagem e entre passe.
Através da atenção cuidadosa a esses fatores, os soldadores podem minimizar o risco de tricas por hidrogênio em aplicações de tubulações.